Ever wondered how power gets from one place to another, especially over long distances or through construction sites? The cables that make this possible are more than just wires—they’re finely engineered systems designed to withstand tough conditions and ensure smooth, reliable transmission. Power cable manufacturing plays a key role in achieving this. In this blog, we’ll explore the technology and engineering behind cable manufacturing and its critical role.
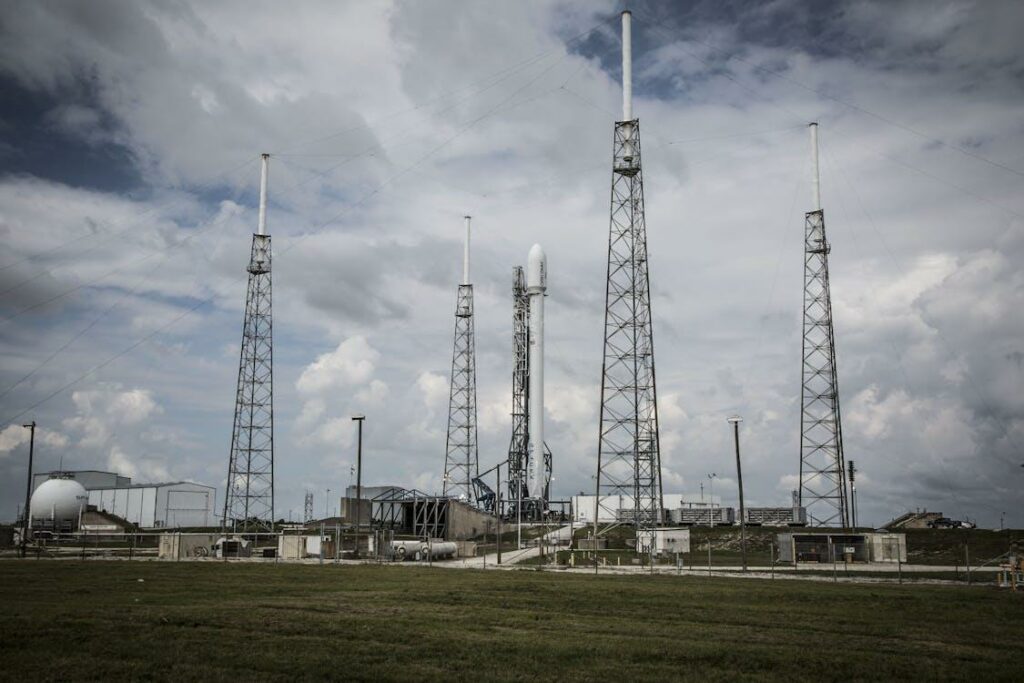
Core Components of Power Cable
To fully understand the complexity of power cable manufacturing, it’s essential to examine the key components that make up these vital systems. Let’s explore each core element in detail.
Conductor
The conductor is the heart of any power cable, responsible for carrying electrical current. Copper and aluminum are the most common materials used for conductors, each offering distinct advantages. Copper, known for its excellent conductivity, is often preferred in situations where high efficiency and minimal energy loss are paramount. However, its higher cost and greater weight are factors to consider. Aluminum, on the other hand, is more lightweight and cost-effective but has lower conductivity. Therefore, high voltage power cable manufacturers must balance these trade-offs to ensure the best performance within budgetary constraints.
Insulation
Insulation is crucial in preventing electrical faults and ensuring safe power transmission. Cross-linked polyethylene (XLPE) is a widely used material for its superior thermal stability and mechanical strength. Ethylene propylene rubber (EPR), another popular choice, offers excellent flexibility and resistance to environmental stressors. Gas-insulated systems are also utilized for high-voltage cables, providing better insulation in compact spaces. Each insulation type is chosen based on voltage requirements, environmental conditions, and the desired lifespan of the cable.
Shielding
Shielding is essential for managing electric fields around the conductor and minimizing electromagnetic interference (EMI). Semiconductor layers, typically made from carbon-loaded polymers, are commonly used in modern cables to control the electric fields. This shielding layer ensures that the power transmission is both stable and safe, especially in densely populated or sensitive areas.
Armor/Sheath
Power cables are often subjected to physical stresses, including crushing forces, abrasion, and exposure to harsh outdoor environments. To protect the internal components, armored layers are applied, typically using steel or aluminum. These metals provide robust mechanical protection. For outdoor applications, UV-resistant polymers, such as high-density polyethylene (HDPE), are used for the outer sheath, shielding the cable from harmful UV rays and environmental wear.
Material
The materials used in power cables are increasingly designed with sustainability in mind. Many power cable suppliers now prioritize recyclable components, such as lead-free sheaths and recyclable XLPE. Additionally, eco-friendly materials like bio-based polymers are gaining traction, reducing the environmental impact of power cables. The use of low-carbon aluminum conductors further enhances the eco-friendliness of modern power cables.
Design Considerations of Power Cable
When designing a power cable, several factors must be taken into account to ensure the cable meets its intended purpose. Each design decision directly impacts the cable’s efficiency, safety, and operational longevity.
Voltage Rating (HV/EHV)
The voltage rating is one of the most critical design considerations. High voltage (HV) and extra-high voltage (EHV) cables are designed to handle significantly more power, with advanced insulation and shielding to ensure safe operation at these levels. High voltage power cable manufacturers must carefully select materials and design parameters to ensure the cable performs effectively over long distances without energy loss.
Ampacity
Ampacity refers to the maximum amount of current a cable can safely carry. It is determined by factors such as conductor size, insulation material, and environmental conditions. Ensuring the right ampacity is essential for maintaining the safety and longevity of the cable.
Resistance to Corona Discharge
Corona discharge occurs when the electric field around the conductor becomes so intense that it ionizes the surrounding air, leading to energy loss and potential cable degradation. Therefore, minimizing corona discharge is a key design consideration, especially for cables operating at higher voltages. Advanced shielding and insulation materials are used to reduce the occurrence of corona discharge.
Power Cable Manufacturing Process
The process of manufacturing power cables is intricate, involving multiple steps to ensure the final product is reliable, safe, and efficient. Each stage focuses on creating a high-quality product that can withstand both electrical and mechanical stresses.
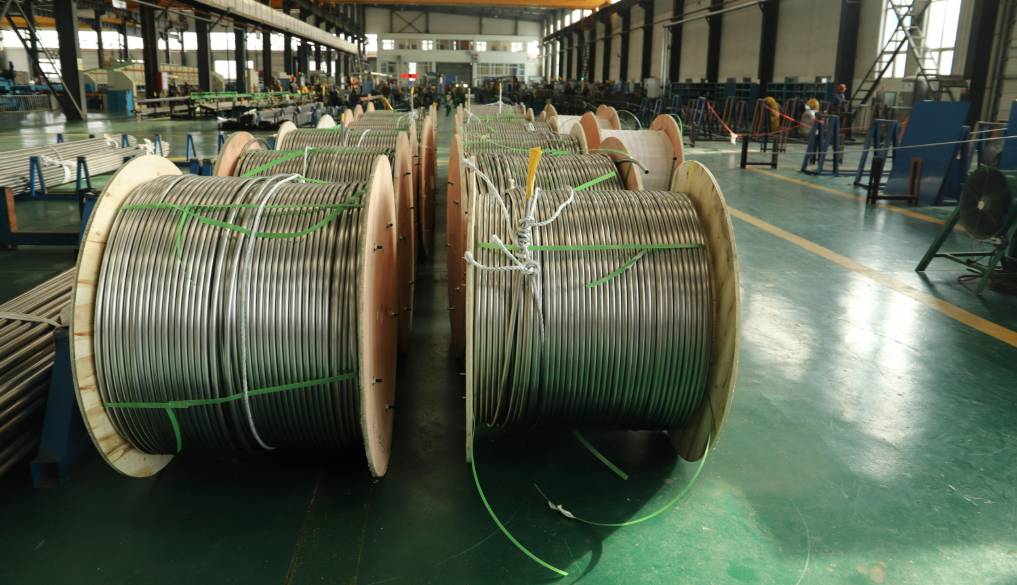
Step 1: Conductor Production
The first step in power cable manufacturing involves producing the conductor. This includes wire drawing, where raw metal is pulled into long strands, and stranding, where these individual wires are twisted together to form the conductor. Compacting the conductor helps to reduce the skin effect, which is the tendency for high-frequency currents to travel on the outer surface of the conductor, ultimately improving electrical efficiency.
Step 2: Insulation Extrusion
Once the conductor is ready, the next step is the extrusion of insulation. A triple-layer extrusion process is used to apply a uniform insulation layer, ensuring there are no voids or weak points. Cross-linking processes, such as steam curing for XLPE, enhance the insulation’s thermal stability, enabling it to withstand higher temperatures and harsh conditions without degrading.
Step 3: Shielding & Sheathing
After insulation, the cable is coated with metallic shields (copper or aluminum tapes) to protect against electrical interference and external damage. Anti-corrosion coatings are also applied to extend the cable’s lifespan. The outer sheath is then extruded, using specialized polymers that offer UV and chemical resistance, particularly for cables used in outdoor or industrial environments.
Step 4: Testing & Quality Control
The final stage of power cable manufacturing involves extensive testing and quality control. Partial discharge tests are performed to detect insulation weaknesses, while hipot (high-potential) testing ensures the cable can handle high voltages. Tensile strength checks are also carried out to verify the mechanical durability of the cable. Compliance with international standards such as IEC 60502, IEEE 386, and ASTM B8 ensures that the cable is fit for its intended use.
Technical Standards & Certifications
Power cables are subject to rigorous technical standards and certifications to ensure safety, reliability, and performance.
Global Standards: IEC, IEEE, and Regional Certifications
Global standards, such as those from the International Electrotechnical Commission (IEC) and Institute of Electrical and Electronics Engineers (IEEE), provide comprehensive guidelines for power cable design, manufacturing, and testing. Regional certifications, such as UL and CE, are also critical for ensuring cables meet local safety and performance requirements.
Key Tests
Several tests are essential in certifying power cables. Thermal cycling simulates the long-term effects of temperature variations on cables, while aging tests accelerate the aging process to assess how cables perform over time. Flame resistance tests, such as IEC 60332, ensure cables can withstand fire hazards, particularly in sensitive environments like tunnels or substations.
Innovations in Power Cable Technology
The field of power cable manufacturing is continuously evolving, with technological advancements leading to more efficient and sustainable cables.
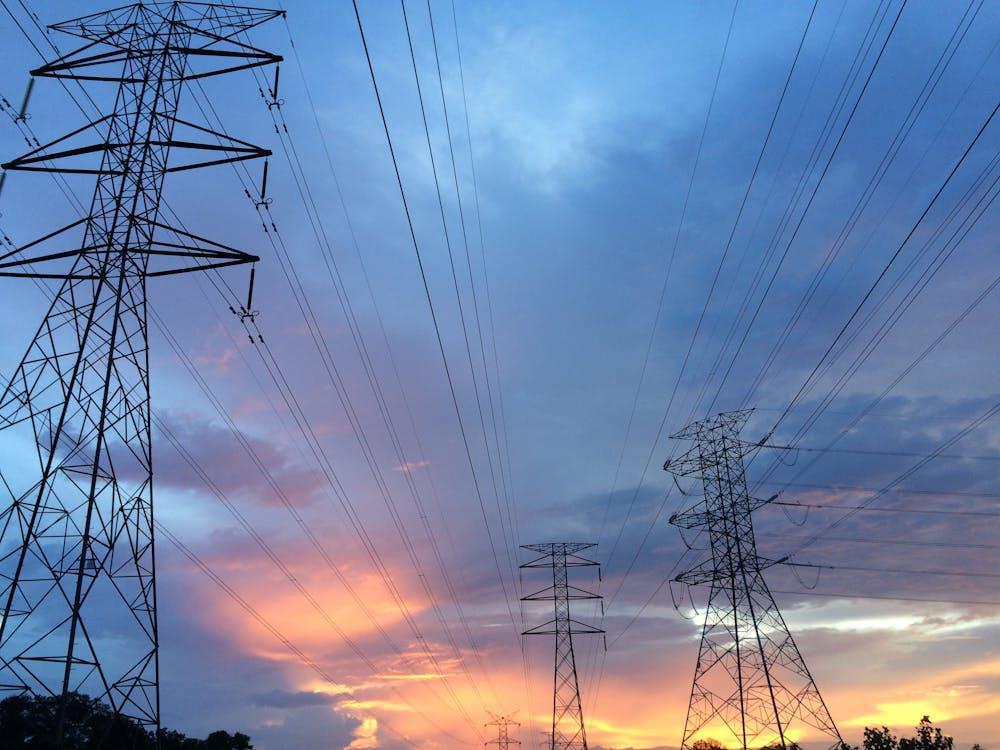
High-Temperature Superconducting (HTS) Cables
HTS cables, made from materials that conduct electricity with zero resistance at extremely low temperatures, offer significant potential for reducing energy loss during long-distance power transmission. These cables can transmit large amounts of electricity with minimal energy dissipation, making them ideal for cross-continental power networks.
Smart Cables
Smart cables integrate fiber optics into their design, enabling real-time monitoring of load and faults. This technology allows for predictive maintenance, identifying potential issues before they lead to failure, and improving the overall reliability of power transmission networks.
HVDC Cables
High-voltage direct current (HVDC) cables are revolutionizing the way renewable energy is transmitted over long distances. HVDC cables allow for the efficient transfer of energy across vast distances, making them an essential component in the global push toward sustainable energy.
Future Trends of Power Cable Manufacturing
The future of power cable manufacturing looks promising, with innovations poised to enhance efficiency, sustainability, and deployment speed.
Modular Cabling
Modular cabling systems, which are pre-fabricated for quick assembly, are becoming increasingly popular for large-scale projects. These systems can reduce installation time and offer greater flexibility in adapting to changing power requirements.
Nanocomposite Insulation
Nanocomposite insulation materials are under development to enhance dielectric strength, allowing cables to operate at higher voltages and in more demanding environments. These materials promise to further increase the efficiency and durability of power cables.
Digital Twins
Digital twin technology, driven by AI, will enable predictive maintenance for cable networks. By creating a virtual replica of the cable system, engineers can monitor performance in real-time and anticipate failures, ultimately extending the lifespan of the infrastructure.
Conclusion
The power cable manufacturing combines advanced materials, precise engineering, and rigorous testing to ensure safe, reliable, and long-lasting performance. As energy demands continue to grow, these innovations will only become more important. If you’re looking for cables that can meet these high standards, connecting with a trusted power cable supplier like LX Cable will help you stay ahead in the ever-evolving field of power transmission.