Dieser Artikel stellt kurz die verschiedenen Arten von Elektrokabeln vor und erklärt, was sie sind und für welche Szenarien sie geeignet sind. So können Sie bei Bedarf die passenden Elektrokabel auswählen. Die drei Haupttypen sind Niederspannungs-, Mittelspannungs- und Hochspannungskabel. Es gibt jedoch noch viele weitere Arten von Elektrokabeln.
Stromkabel
Stromkabel sind speziell für die Übertragung von elektrischem Strom konzipiert. Sie werden nach Nennspannung, Konstruktion und Einsatzzweck kategorisiert. Das Verständnis dieser Kategorien ist für eine sichere und effiziente Stromverteilung von grundlegender Bedeutung.
Niederspannungskabel
Niederspannungskabel sind für Anwendungen mit relativ niedriger Spannung (typischerweise bis zu 1000 V Wechselstrom) konzipiert. Sie sind die Hauptlastkabel für elektrische Anlagen in Wohngebäuden und kleineren Gewerbebetrieben.
- Gängige TypenEinadrige Leitungen, mehradrige Kabel (Mantelleitungen), Flachkabel und flexible Leitungen sind gängige Beispiele. Einadrige Leitungen bestehen, wie der Name schon sagt, aus einem einzelnen, isolierten Leiter. Mehradrige Kabel, oft auch Mantelleitungen genannt, enthalten zwei oder mehr isolierte Leiter, die in einem äußeren Schutzmantel gebündelt sind. Flachkabel haben parallel zueinander angeordnete Leiter und werden häufig für spezielle Anwendungen wie die Geräteverkabelung verwendet. Flexible Leitungen sind für Anwendungen konzipiert, die Bewegung und Flexibilität erfordern, wie z. B. Netzkabel für tragbare Geräte.
- DämmstoffeZu den üblicherweise für Niederspannungskabel verwendeten Isoliermaterialien gehören Polyvinylchlorid (PVC) und vernetztes Polyethylen (XLPE). PVC ist ein kostengünstiger und vielseitiger thermoplastischer Kunststoff mit guten elektrischen Isoliereigenschaften und hoher Flexibilität. XLPE ist ein duroplastischer Kunststoff, der im Vergleich zu PVC bessere thermische und elektrische Eigenschaften bietet, darunter höhere Betriebstemperaturen und eine bessere Abrieb- und Chemikalienbeständigkeit.
- AnwendungenNiederspannungskabel sind im Alltag allgegenwärtig und versorgen Haushaltsgeräte wie Kühlschränke, Waschmaschinen und Fernseher mit Strom. Sie werden auch häufig für Beleuchtungskreisläufe in Wohnhäusern, Büros und Gewerbegebäuden eingesetzt. Darüber hinaus versorgen sie verschiedene kleine elektrische Geräte und Anlagen mit Strom.
- Eigenschaften: Diese Kabel zeichnen sich im Allgemeinen durch ihren einfachen Aufbau und die relativ geringen Kosten aus, was sie für zahlreiche Anwendungen zu einer wirtschaftlichen Wahl macht. Sie sind außerdem relativ einfach zu installieren und zu handhaben.
Mittelspannungskabel
Mittelspannungskabel arbeiten typischerweise bei Spannungen zwischen 1 kV und 35 kV. Diese Kabel sind für die Stromverteilung von Umspannwerken zu Industrieanlagen und städtischen Verteilnetzen von entscheidender Bedeutung.
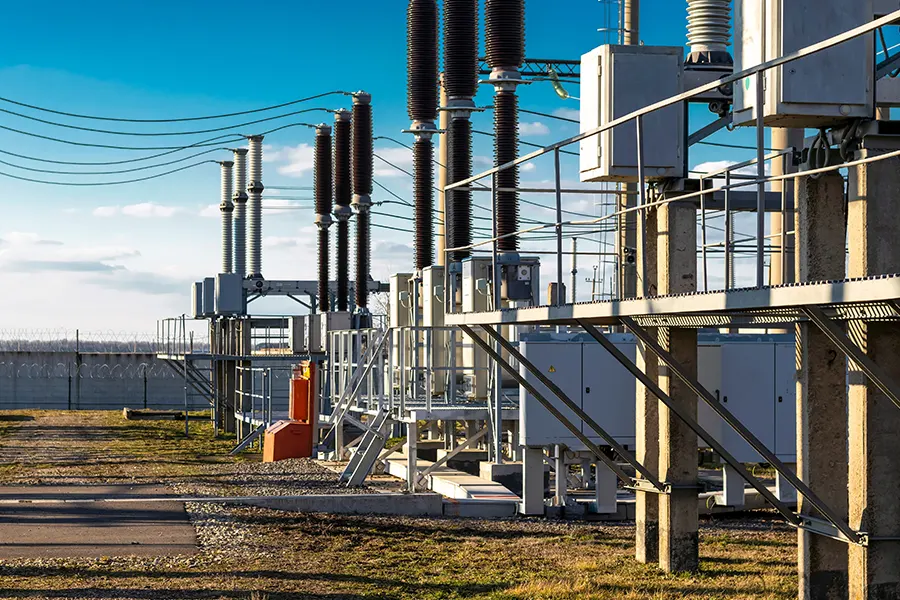
- Spannungsbereich: Normalerweise im Bereich von 1 kV bis 35 kV.
- Konstruktionsmerkmale: Diese Kabel sind komplexer aufgebaut als Niederspannungskabel und bestehen häufig aus einem Leiterschirm, einer Isolationsschicht, einem Isolationsschirm, einem Metallschirm (Kupferband oder -drähte) und einem Außenmantel. Der Leiterschirm sorgt für ein gleichmäßiges elektrisches Feld um den Leiter, während der Isolationsschirm eine ähnliche Funktion für die Außenfläche der Isolierung erfüllt. Der Metallschirm dient als Ableiter für Fehlerströme und trägt zur Eindämmung des elektrischen Feldes bei.
- AnwendungenMittelspannungskabel werden häufig in städtischen Stromverteilungsnetzen eingesetzt, um Transformatoren mit Strom zu versorgen, die die Spannung für den lokalen Gebrauch heruntertransformieren. Auch in Industrieanlagen sind sie für die Stromversorgung großer Maschinen und Geräte unverzichtbar.
- Eigenschaften: Diese Kabel weisen im Vergleich zu Niederspannungskabeln eine höhere Isolationsleistung und mechanische Festigkeit auf, um den höheren elektrischen Belastungen und Umweltbedingungen standzuhalten, die mit Mittelspannungsanwendungen verbunden sind.
Hochspannungskabel
Hochspannungskabel sind für die Übertragung von Strom mit Spannungen zwischen typischerweise 35 und 230 kV ausgelegt. Sie spielen eine wichtige Rolle bei der Stromübertragung über große Entfernungen und der Anbindung großer Umspannwerke.
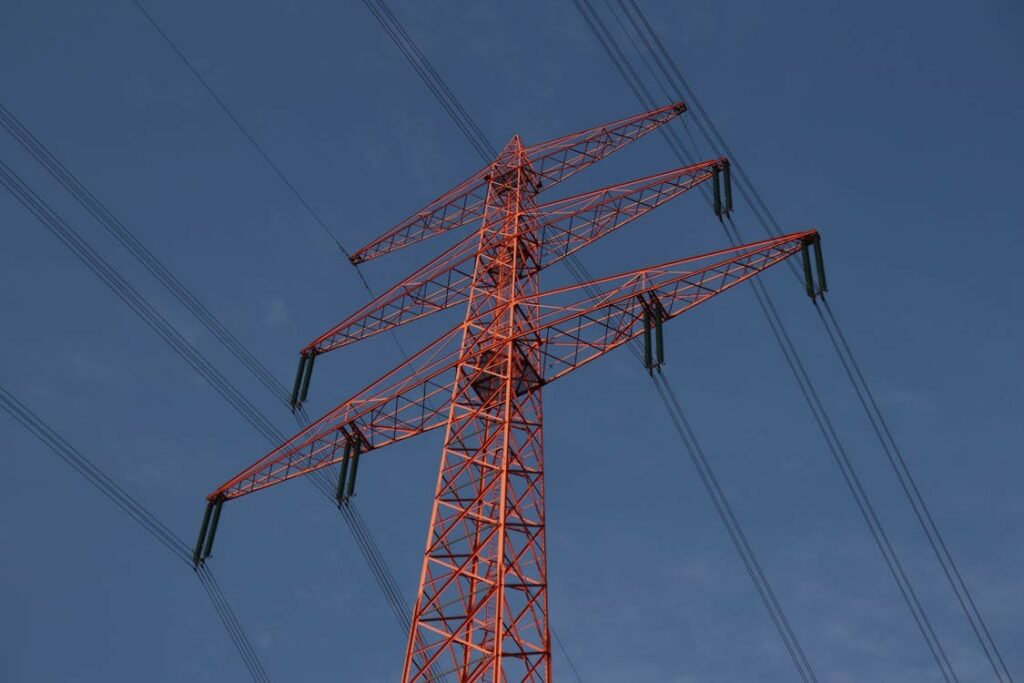
- Spannungsbereich: Typischerweise über 35 kV und bis zu 230 kV.
- Konstruktionsmerkmale: Hochspannungskabel verfügen im Vergleich zu Mittelspannungskabeln über noch ausgefeiltere Isolations- und Abschirmstrukturen. Diese umfassen beispielsweise mehrere Schichten Isoliermaterial, fortschrittliche Abschirmkonstruktionen zur Beherrschung der starken elektrischen Felder und robuste Außenmäntel zum Schutz vor der Umwelt.
- Anwendungen: Diese Kabel dienen in erster Linie der effizienten Übertragung großer Mengen elektrischer Energie über weite Entfernungen und verbinden Kraftwerke mit großen Lastzentren. Sie sind außerdem wichtige Komponenten in großen Umspannwerken.
- Eigenschaften: Hochspannungskabel zeichnen sich durch ihre extrem hohe Isolationsleistung und die hohen Sicherheitsanforderungen aufgrund der hohen Spannungen aus, die sie übertragen. Fortschrittliche Materialien und Fertigungstechniken gewährleisten ihre Zuverlässigkeit und Langlebigkeit.
Höchstspannungskabel
Höchstspannungskabel (HöH) arbeiten auf den höchsten Spannungsebenen, typischerweise über 230 kV. Sie stellen den neuesten Stand der Stromübertragungstechnologie dar und sind für landesweite Stromnetze von entscheidender Bedeutung.
- Spannungsbereich: Normalerweise über 230 kV.
- Technische Herausforderungen und InnovationenDie Entwicklung und der Einsatz von Höchstspannungskabeln stellen erhebliche technische Herausforderungen dar, darunter die Beherrschung extrem hoher elektrischer Belastungen, die Minimierung von Leistungsverlusten über große Entfernungen sowie die Gewährleistung der Zuverlässigkeit und Sicherheit des Systems. In diesem Bereich werden kontinuierlich Innovationen in den Bereichen Materialwissenschaft, Kabeldesign und Installationstechnik erzielt.
- Anwendungen: Höchstspannungskabel werden vorwiegend für landesweite Stromnetze eingesetzt und ermöglichen die Übertragung großer Mengen Strom über große geografische Gebiete. Sie verbinden große Stromerzeugungsanlagen mit weit entfernten Lastzentren und erhöhen so die Stabilität und Effizienz der nationalen Strominfrastruktur.
- Eigenschaften: Diese Kabel stellen die fortschrittlichste elektrische Kabeltechnologie dar und beinhalten hochmoderne Materialien und Designs, um die extremen Spannungspegel zu bewältigen und einen minimalen Energieverlust während der Übertragung zu gewährleisten.
Spezialkabel
Hochtemperaturkabel
Hochtemperaturkabel sind so konzipiert, dass sie extremer Hitze ohne Qualitätsverlust standhalten. Sie werden aus speziellen Isoliermaterialien hergestellt, um einen sicheren Betrieb bei erhöhten Temperaturen zu gewährleisten.
Funktionen und Anwendungen: Wird in Öfen, Brennöfen, industriellen Heizgeräten und anderen Hochtemperaturumgebungen verwendet.
Flammhemmende Kabel
Flammhemmende Kabel sind so konzipiert, dass sie der Ausbreitung von Feuer entgegenwirken. Sie können zwar brennen, verbreiten die Flamme jedoch nicht und erhöhen so die Sicherheit im Brandfall.
- Funktionen und Sicherheitsbedeutung: Entscheidend zur Verhinderung der Brandausbreitung in Gebäuden und geschlossenen Räumen.
- Gemeinsame Standards und Klassifizierungen: IEC 60332, UL 1581 usw.
- Anwendungen: Gebäude, öffentliche Bereiche, Transportsysteme.
Wasserdichte Kabel
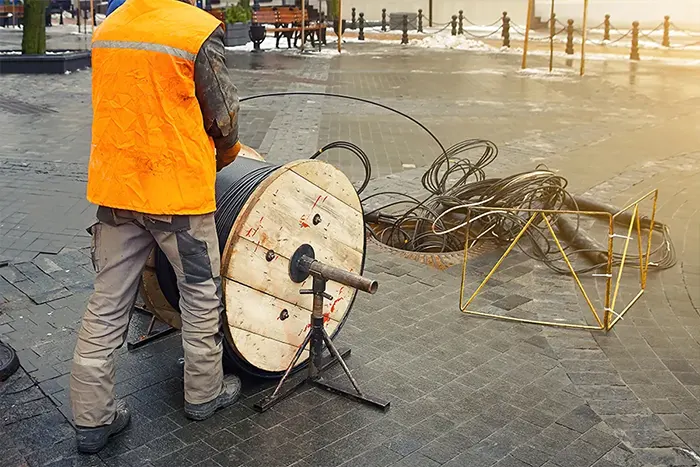
Wasserdichte Kabel sind speziell dafür konzipiert, das Eindringen von Wasser zu verhindern und gewährleisten so eine zuverlässige Leistung in nassen oder unter Wasser liegenden Umgebungen. Ihr Schutzgrad wird häufig durch die IP-Schutzart angegeben.
- Funktionen und Schutzstufen: Hohe Beständigkeit gegen Wasser und Feuchtigkeit (z. B. IP67, IP68).
- Anwendungen: Außeninstallationen, Unterwasserausrüstung, Schiffsanwendungen.
Flexible/Schleppkettenkabel
Flexible Kabel oder Schleppkettenkabel sind dafür ausgelegt, ständigem Biegen und Verbiegen in dynamischen Anwendungen standzuhalten und verfügen über eine spezielle Konstruktion für eine lange Lebensdauer bei ständiger Bewegung.
- Eigenschaften und Biegeleistung: Hohe Flexibilität, Abrieb- und Verschleißfestigkeit.
- Anwendungen: Robotik, automatisierte Maschinen, Fördersysteme.
Komponenten eines Elektrokabels
Das Verständnis der einzelnen Komponenten eines Elektrokabels ist entscheidend, um dessen Gesamtfunktion zu verstehen und das passende Kabel für eine bestimmte Anwendung auszuwählen. Jede Schicht spielt eine entscheidende Rolle für die sichere und effiziente Übertragung von Strom oder Signalen.
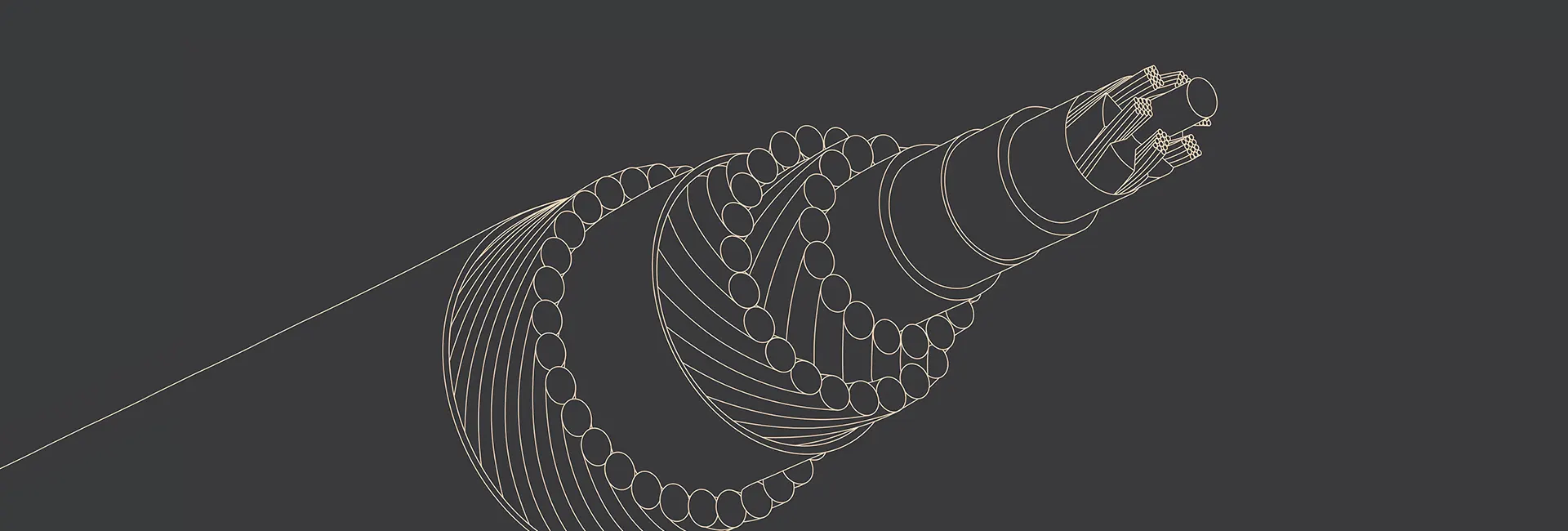
Leiter
Der Leiter ist das Herzstück des Elektrokabels und dient als Pfad für den Fluss des elektrischen Stroms oder der Signale.
- Funktion: Zur Übertragung von elektrischem Strom oder Signalen. Die Effizienz dieser Übertragung hängt vom Material und der Größe (Querschnitt) des Leiters ab. Ein größerer Querschnitt führt im Allgemeinen zu einem geringeren Widerstand und somit zu einem geringeren Leistungsverlust über eine bestimmte Distanz.
- Gängige MaterialienDie am häufigsten für Leiter verwendeten Materialien sind Kupfer und Aluminium. Kupfer ist hochleitfähig, dehnbar (leicht zu Drähten zu ziehen) und korrosionsbeständig, weshalb es trotz seiner höheren Kosten für viele Anwendungen die bevorzugte Wahl ist. Aluminium ist leichter und günstiger als Kupfer, weist aber eine geringere Leitfähigkeit auf, sodass für die gleiche Stromstärke ein größerer Querschnitt erforderlich ist. Aluminium wird häufig in Freileitungen verwendet, bei denen das Gewicht eine wichtige Rolle spielt.
Isolierung
Die Isolierschicht umgibt den Leiter und ist entscheidend für die Verhinderung von Stromlecks und Kurzschlüssen, gewährleistet die Sicherheit des elektrischen Systems und verhindert unbeabsichtigte Strompfade.
- Funktion: Um das Austreten von elektrischem Strom aus dem Leiter zu verhindern und Kurzschlüsse zwischen benachbarten Leitern oder zwischen einem Leiter und der Erde zu vermeiden. Die Isolierung muss der am Leiter anliegenden Spannung standhalten können, ohne zusammenzubrechen.
- Gängige MaterialienZur Isolierung werden verschiedene Polymermaterialien verwendet, jedes mit spezifischen Eigenschaften für unterschiedliche Anwendungen. PVC (Polyvinylchlorid) ist eine gängige und kostengünstige Option mit guter Flexibilität und elektrischer Isolierung. XLPE (vernetztes Polyethylen) bietet hervorragende thermische und elektrische Eigenschaften, darunter höhere Betriebstemperaturen und eine bessere Beständigkeit gegen Chemikalien und Abrieb. Gummi, darunter Materialien wie Neopren und Silikon, bietet hervorragende Flexibilität und Beständigkeit gegen extreme Temperaturen und raue Umgebungen. Für spezielle Hochleistungsanwendungen werden weitere spezielle Isoliermaterialien eingesetzt.
Füllstoff (optional)
Füllstoffe sind nichtleitende Materialien, die in mehradrigen Kabeln zum Füllen der Zwischenräume zwischen den isolierten Leitern verwendet werden. Sie sind zwar optional, erfüllen aber mehrere wichtige Funktionen.
- Funktion: Füllt die Lücken zwischen den isolierten Leitern und macht das Kabel dadurch kompakter und runder. Dies trägt dazu bei, die Form des Kabels zu erhalten, verleiht den inneren Adern mechanische Stabilität und verhindert, dass sich die Leiter durch Biegen oder Verdrehen verschieben oder beschädigt werden.
- Gängige Materialien: Gängige Füllmaterialien sind verschiedene Fasern (wie Jute oder Baumwolle), Kunststoffverbindungen und extrudierte Polymermaterialien. Die Wahl des Füllmaterials hängt vom Anwendungsbereich des Kabels und den gewünschten mechanischen und thermischen Eigenschaften ab.
Innenhülle (optional)
Ein Innenmantel ist eine zusätzliche Schutzschicht, die über den isolierten Leitern und etwaigen Füllstoffen angebracht wird. Er ist nicht immer vorhanden, bietet aber bei bestimmten Kabelkonstruktionen erhebliche Vorteile.
- Funktion: Bietet eine zusätzliche Schutzschicht für die Isolierung der einzelnen Leiter. Sie bietet erhöhte mechanische Festigkeit und schützt die Isolierung vor Abrieb und mechanischen Beschädigungen während der Installation und Nutzung. Darüber hinaus bieten einige Innenmäntel eine verbesserte Beständigkeit gegen Feuchtigkeit und Chemikalien und schützen so die inneren Komponenten des Kabels zusätzlich.
- Gängige Materialien: Gängige Materialien für Innenhüllen sind PVC (Polyvinylchlorid) und PE (Polyethylen). Diese Materialien bieten ein ausgewogenes Verhältnis zwischen Flexibilität, mechanischer Festigkeit und Beständigkeit gegen Umwelteinflüsse.
Abschirmung (optional)
Die Abschirmschicht ist eine leitfähige Schicht, die die isolierten Leiter oder den inneren Mantel umgibt. Ihr Hauptzweck besteht darin, elektromagnetische Störungen (EMI) und Hochfrequenzstörungen (RFI) zu minimieren, die die Leistung empfindlicher elektronischer Geräte oder die über das Kabel übertragenen Signale beeinträchtigen können.
- Funktion: Reduziert elektromagnetische Störungen (EMI) und Hochfrequenzstörungen (RFI) durch eine leitfähige Barriere, die diese unerwünschten Signale abfängt und erdet. Dies gewährleistet die Integrität der über das Kabel übertragenen elektrischen Energie oder Daten und verhindert, dass das Kabel Störungen mit benachbarten elektronischen Geräten verursacht.
- Gängige Typen: Es gibt verschiedene Abschirmungsarten, darunter Kupferband-, Aluminiumfolien- und Geflechtschirme aus Kupfer- oder Aluminiumdrähten. Die Wahl der Abschirmungsart hängt von der Frequenz und Intensität der zu erwartenden Störungen sowie den Flexibilitätsanforderungen des Kabels ab. Geflechtschirme bieten hohe Flexibilität und Haltbarkeit, während Folienschirme eine hervorragende Abdeckung bieten und hochfrequente Störungen wirksam abschirmen.
Rüstung (optional)
Die Panzerschicht ist eine robuste Schutzhülle für Kabel, die mechanischer Beanspruchung oder physischen Beschädigungen ausgesetzt sind. Sie bietet erheblichen Schutz vor Stößen, Quetschkräften und Abrieb.
- Funktion: Bietet zusätzlichen mechanischen Schutz für das Kabel und schützt die inneren Komponenten vor äußeren Einflüssen wie Stößen, Quetschungen und Abrieb. Panzerte Kabel sind in Umgebungen unerlässlich, in denen das Kabel rauen Bedingungen oder versehentlichen Beschädigungen ausgesetzt sein kann.
- Gängige TypenGängige Panzerungsarten sind Stahlbandpanzerung (STA) und Stahldrahtpanzerung (SWA). STA besteht aus ein oder zwei Lagen Stahlband, die spiralförmig um die inneren Kabelschichten gelegt werden und so guten mechanischen Schutz bieten. SWA besteht aus einer Lage verzinkter Stahldrähte, die eine noch höhere Zugfestigkeit und Schutz vor Quetschkräften bieten. Die Wahl zwischen STA und SWA hängt von den spezifischen mechanischen Belastungen ab, denen das Kabel standhalten soll.
Außenmantel
Der Außenmantel ist die äußerste Schicht des Kabels und schützt alle internen Komponenten umfassend vor Umwelteinflüssen, Abrieb und anderen äußeren Einflüssen. Er ist die erste Verteidigungslinie des Kabels.
- Funktion: Zum Schutz der inneren Kabelkomponenten vor Umwelteinflüssen wie Feuchtigkeit, Chemikalien, UV-Strahlung und Abrieb. Es bietet außerdem einen gewissen mechanischen Schutz und trägt dazu bei, die Integrität des Kabels über seine gesamte Lebensdauer zu erhalten.
- Gängige MaterialienGängige Materialien für Außenmäntel sind PVC (Polyvinylchlorid), PE (Polyethylen) und PUR (Polyurethan). PVC ist ein vielseitiges und kostengünstiges Material mit guter Abrieb-, Feuchtigkeits- und Chemikalienbeständigkeit. PE bietet hervorragende Feuchtigkeits- und Witterungsbeständigkeit. PUR bietet hervorragende Abriebfestigkeit, Flexibilität sowie Beständigkeit gegen Öle und Chemikalien und eignet sich daher für anspruchsvolle Industrieanwendungen. Die Wahl des Außenmantelmaterials hängt von den spezifischen Umgebungsbedingungen ab, denen das Kabel ausgesetzt ist, und dem erforderlichen Schutzniveau.
Zu berücksichtigende Faktoren bei der Auswahl von Elektrokabeln
-
Elektrische Parameter
- Nennspannung: Die maximale Spannung, für die das Kabel ausgelegt ist.
- Strombelastbarkeit/Strombelastbarkeit: Der maximale Strom, den das Kabel kontinuierlich führen kann, ohne dass die zulässige Temperatur überschritten wird.
- Impedanz: Der Widerstand gegen den Wechselstromfluss. Wichtig für Signalübertragungskabel.
-
Umgebungsbedingungen
- Betriebstemperatur: Der Temperaturbereich, dem das Kabel während des Betriebs ausgesetzt ist.
- Luftfeuchtigkeit: Der Feuchtigkeitsgrad in der Umgebung.
- Chemische Korrosion: Mögliche Belastung durch ätzende Substanzen.
- Mechanische Beanspruchung: Gefahr von Abrieb, Quetschung, Biegung oder Spannung.
- Bedarf an flammhemmenden, wasserdichten und UV-beständigen Eigenschaften: Spezifische Umweltanforderungen.
-
Sicherheitsstandards und -vorschriften
- Einhaltung lokaler und internationaler Sicherheitsstandards: Sicherstellung der Einhaltung relevanter Sicherheitsvorschriften (z. B. IEC, UL, CSA).
- Kabelprüfzeichen: Achten Sie auf Zertifizierungszeichen, die die Einhaltung von Standards belegen.
-
Installation und Wartung
- Anforderungen an den Biegeradius: Der minimale Radius, in dem das Kabel gebogen werden kann, ohne beschädigt zu werden.
- Verbindungsmethoden: Kompatibilität mit Abschlussmethoden und Anschlüssen.
- Einfache zukünftige Wartung: Zugänglichkeit für Inspektionen und eventuelle Reparaturen.
-
Kosteneffizienz
- Anschaffungskosten: Der Preis des Kabels selbst.
- Installationskosten: Für die Installation erforderliche Arbeitskräfte und Materialien.
- Langfristige Betriebskosten: Mögliche Energieverluste und Ersatzkosten.
Abschluss
In diesem Artikel haben wir die verschiedenen Arten von Elektrokabeln und ihre jeweiligen Anwendungen untersucht. Bei der Auswahl des passenden Kabeltyps sollten spezifische Anforderungen wie Spannung und Umgebungsbedingungen berücksichtigt werden. Auch Faktoren wie Installations- und Wartungskosten sind wichtig, um die Effizienz zu steigern, Kosten zu senken und die Sicherheit zu erhöhen.
LX CABLE: Produkte und Dienstleistungen
LX-KABEL ist ein professioneller Kabelhersteller, der in den 1990er Jahren gegründet wurde. Wir sind spezialisiert auf die Herstellung und den Verkauf Stromkabel, Freileitungen, elektrische Leitungen, Photovoltaikkabel und GlasfaserkabelWir bieten auch OEM-Dienstleistungen an und bieten Lösungen für verschiedene Elektroprojekte, wodurch die Beschaffung optimiert und die Projekteffizienz gesteigert wird.
Häufig gestellte Fragen
Stromkabel werden in Niederspannungs-, Mittelspannungs- und Hochspannungskabel unterteilt. Zu den Spezialtypen gehören Panzerkabel, flexible Kabel und Tauchkabel, die jeweils für spezifische Anwendungen und Umgebungen konzipiert sind.
Sie werden auch als Hochspannungskabel (HT) und Niederspannungskabel (LT) bezeichnet. Die weitere Kategorisierung von LT- und HT-Kabeln erfolgt wie folgt: Nennspannung: LT-Kabel haben eine Nennspannung von 660 V bis 1100 V. Kabel mit einer Nennspannung von über 3300 V (33 kV) werden als HT-Kabel bezeichnet.
Twisted Pair-, Koaxial- und Glasfaserkabel sind die drei wichtigsten Netzwerkkabeltypen in Kommunikationssystemen. Sie unterscheiden sich in Aufbau, Geschwindigkeit, Bandbreite und Anwendung.
Je nach Aufbau und Verwendungszweck gibt es hauptsächlich drei Kabeltypen: Elektrokabel, Stromkabel und Computerkabel. In diesem Physikartikel untersuchen wir die verschiedenen Kabeltypen und ihre Anwendungen.
Ein 3-adriges Kabel besteht typischerweise aus drei einzeln isolierten massiven Adern für einen Neutralleiter, einen Phasenleiter und einen Erdleiter. Diese sind mit einer äußeren PVC-Schutzhülle umhüllt, deren Farbe variieren kann.
Einfach ausgedrückt: Hochspannungskabel sind für höhere Spannungen ausgelegt, typischerweise 11 kV und mehr. Sie haben eine dickere Isolierung und dickere Leiter. Niederspannungskabel sind für bis zu 1,1 kV ausgelegt und haben eine dünnere Isolierung und dünnere Leiter.
HT-Kabel sind Hochspannungskabel. Sie dienen der Stromübertragung bei hoher Spannung. Ein Kabel besteht aus einem Leiter und einer Isolierung und eignet sich für die Verlegung unter der Erde oder unter Wasser.